The intense laser offers great potential
Development of new procedures for the save disarming of explosive devices to protect base camps
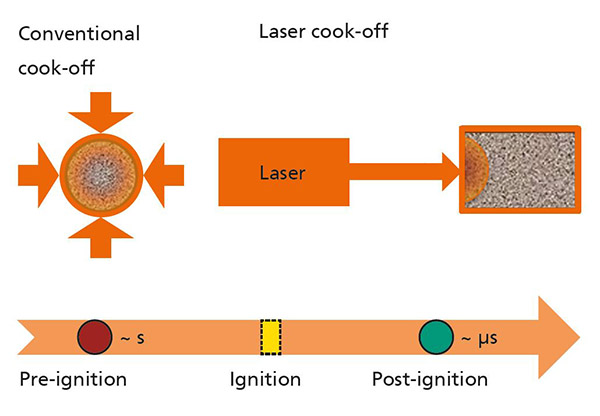
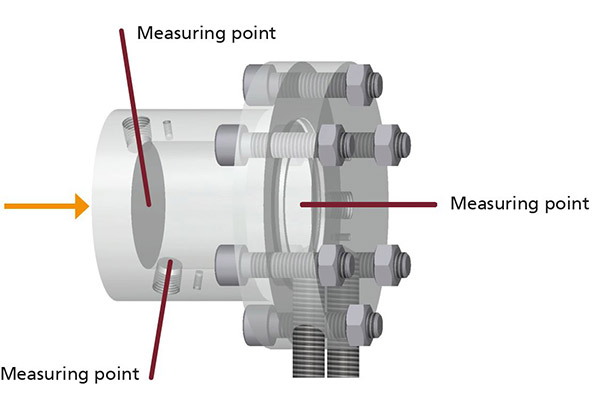
The examination of the effect of intense laser radiation on energetic materials is of considerable importance for security and defense research. The application of high-power lasers offers, among others, great potential in the development of new procedures for the safe disarming of explosive devices, and in defense against mortar shells and rockets in military camps. The thereby occurring processes could not yet be adequately described so far and were recently experimentally and numerically compiled in a doctoral thesis.
The laser cook-off
In order to assess the safety risk of explosive materials during a fire, certain cook-off tests are established, in which energetic materials are slowly heated until the point of thermal ignition (Figure 1). Analogously, the heating of energetic materials with a high-power laser is also considered a laser cook-off. In contrast to a conventional cook-off, the laser causes a local heating with a higher heating rate. This in turn entails a higher temperature gradient in the energetic material.
A cook-off begins with the pre-ignition phase (Figure 1), in which the energetic material is heated and an exothermic reaction begins and chemical energy is released. This reaction becomes self-sustaining the moment when more chemical energy is released than can be dissipated. This marks the time point of thermal ignition. The following post-ignition phase is characterized by the fast conversion of the still unspent energetic material. The quick release and expansion of gaseous reaction products characterizes the explosive mechanical impact of energetic materials. While it is of interest if and when an ignition occurs in the pre-ignition phase, in the post-ignition phase, the question of the reaction strength is in the focus.