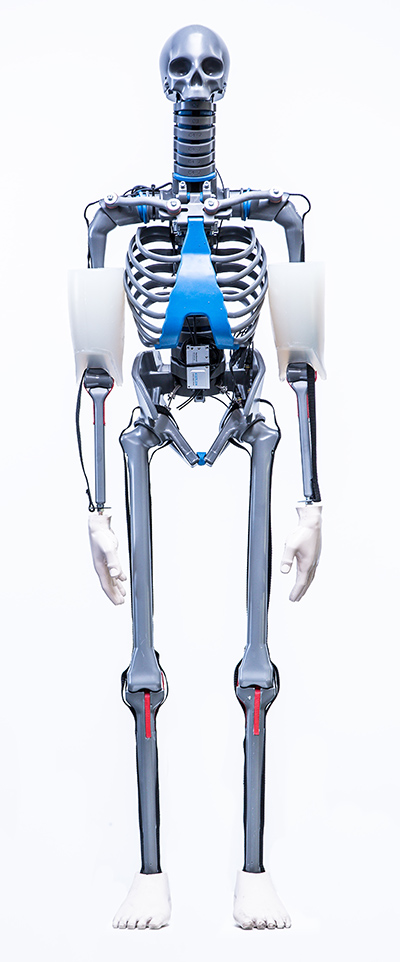
How does the human thorax behave under the impact of dynamic loads? This question is of crucial importance for many areas of research. Be it in the development of new safety technologies in the automotive sector or the testing of new protective clothing in defense research. Researchers at Fraunhofer EMI are working on methods to make the results of such tests more accurate and meaningful.
The further development of dummies by means of additive manufacturing
This goal is achieved through the further development of a new, innovative dummy the bone structures of which are based as closely as possible on the human body. Marcin Jenerowicz from the Human Body Dynamics working group and other scientists from the Additive Design and Manufacturing group at the Fraunhofer Institute for High-Speed Dynamics, Ernst-Mach-Institut. EMI, are taking on the challenge of producing rib bone surrogates using 3D printing processes. The surrogates are intended to provide information about when and under which forces structures of the human thorax undergo damage.
The PRIMUS breakable dummy of the Crash Test Service GmbH (CTS) company is already used in various fields as an anthropomorphic test device (ATD). The CTS dummy (50-percentile male surrogate, M50) is able to represent authentic vehicle damage as well as damage to its own structural components in order to find a match between dummy damage and injury probability. However, to date, only crash validation tests have been conducted to represent the validity and global structural behavior (trajectory, damage to internal and external structures) of the dummy for specific accident outcomes.