Satellites from the 3D printer – A vision becomes reality
Through the use of additive manufacturing techniques – better known as 3D printing – completely new design possibilities arise in the development of satellite components. Within the development of the nanosatellite ERNST, scientists at Fraunhofer EMI have designed and manufactured an optical bench by using a 3D printing process for metals. The optical bench serves as a mounting for different components such as an infrared camera and lens systems. The design of the optical bench was created by using intelligent optimization algorithms. By specifying the loading scenarios, the algorithm is able to calculate an optimized bionic-looking structure.


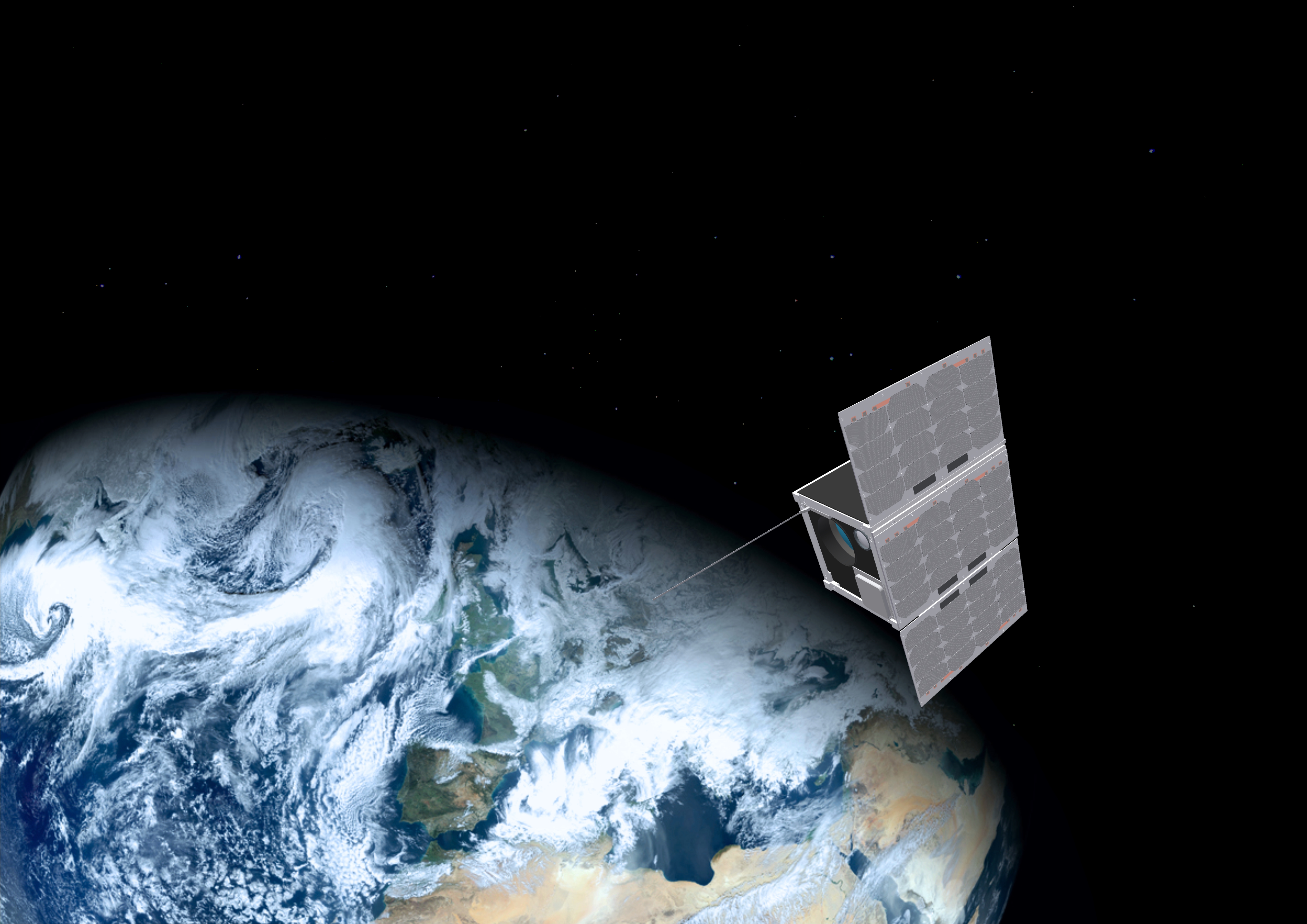
We notice that satellites have become essential in our daily lives. From Earth observation applications and weather forecasting to navigation and communication applications, the use of satellites is indispensable. Especially in the context of industry 4.0, innovative satellite-based applications are of great interest. In order to promote developments and applications in satellite technology even more, the use of so-called small satellites represents enormous potential. Of particular interest are nano- and microsatellites with masses between 10 and 100 kilograms. Unlike the development in standard satellites with masses of several hundred kilograms, which typically take many years to develop, small-scale satellites can be realized in a fraction of the time. This results in a much faster innovation cycle.
3D printing as a manufacturing technology
The further development of additive manufacturing processes, from use in prototypes to production technology for end products, carries tremendous development potential. For example, completely new designs can be created which are no longer subject to the restrictions of conventional manufacturing processes. In addition, assembly operations can be reduced by integrating multiple components in a single component. Since additive manufacturing only generates material where it is needed, a further added value is its high resource-saving potential.
ERNST as a technology driver
ERNST is a 15 kilogram, shoebox-sized nanosatellite that carries an infrared camera for Earth observation as the main payload. ERNST is the acronym for “Experimental SpacecRaft based on Nano-Satellite-Technology”. For the development of the ERNST nanosatellite at Fraunhofer EMI, the so-called “selective laser melting” (SLM) method for additive manufacturing of the optical bench was used. With this technology, highly complex metallic component structures can be manufactured and then installed in the satellite. The special feature of the additively produced optical bench is its design. With the help of multidisciplinary design optimization, a structure could be found which is optimally adapted to the occurring mechanical and thermal loads during the start and the operating phase, and which additionally integrates different functions into a single structure. Therefore, additive manufacturing processes are of great importance for space travel in particular: Highly specialized and individualized lightweight components with completely new shapes enable the integration of additional functions in a small space. With the planned start of ERNST in 2021, an additively manufactured metallic structure will travel on a nanosatellite of this size for the first time.