Safe joint connections under very high-rate loading
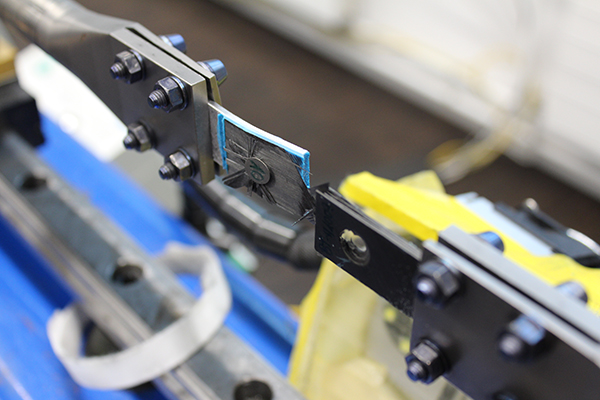
Military aircrafts are subjected to very high-rate loading, as for example high-velocity impacts or blast loads. In order to design safely these types of structures, it is important not only to characterize the materials but also the joints connecting the different parts. However, for the relevant high loading rates, the high-rate servo-hydraulic testing machines cannot provide reliable oscillation-free load-displacement curves.
For this reason, a high-rate material testing device, the “split Hopkinson tension bar”, has been adapted at Fraunhofer EMI in order to enable the testing of aviation representative joints. For this purpose, samples made of typical aircraft material, carbonfiber reinforced plastics (CFRP) and aluminum, have been manufactured. During the first test campaign on the adapted device, three kinds of joints have been tested successfully: bonded, mechanically fastened and hybrid bonded-mechanically fastened. Thus, realizing tests with the split Hopkinson tension bar constitutes an adequate method for the high-rate characterization of joints. The obtained results demonstrate furthermore the potential relevance of hybrid joints to increase the safety of aircrafts: These types of joints both withstand high forces and absorb much energy until failure. Further joints will be characterized in the future using the developed setup.