Clean Sky 2
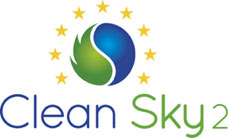
Fraunhofer EMI participates in the largest European aviation research program
Aviation is supposed to generate lower emissions, be more fuel-efficient and more friendly to the environment – this is the goal of leading aviation enterprises and research institutions within the EU Project “Clean Sky”. 75 percent less CO2, 90 percent less NOX, 65 percent less aircraft noise: Clean Sky wants to develop technologies which decisively contribute to more environmentally compatible aircraft and lower-emission air traffic. The intended goal is also to enhance competitiveness and mobility in Europe. From 2020 onwards, the newly developed components are expected to be integrated into demonstrators and then be tested for airworthiness.
To achieve these goals, major industrial companies from the European aviation sector and the European Union have teamed up in a partnership: the Joint Technology Initiative (JTI) Clean Sky. The years from 2014 to 2014 encompass the second phase Clean Sky 2 within the EU Framework Programme for Research and Innovation Horizon 2020. Fraunhofer-Gesellschaft ist part of this joint undertaking.
In close consultation and collaboration with its industrial partners, Fraunhofer EMI takes part in Clean Sky 2. Our scientists develop 3D-printed metallic structures, investigate the effects of hail and lightning strike on aircraft structures, design helicopter structures for bird strike protection and test micro-debris impact on new lightweight structures.
Fraunhofer EMI not only undertakes technological development assignments, but also management tasks within the Clean Sky program: Dr. Stephanie Günther represents the Fraunhofer-Gesellschaft within the Steering Committee of the Airframe Integrative Technology Demonstrator (ITD), Dr. Michael May coordinates the Fraunhofer activities concerning High Versatility and Cost Efficiency (HVC) within the Airframe ITD.
For further information, visit http://www.cleansky.eu/